Multi-directional effluent routing can be selected in the PSM recipe. This provides for simplified re-use or re-purpose of dense slurry and rinse streams.
Localized slip stream temperature, pad thickness, and effluent electrochemistry instrumentation options can be added, data acquisition, analytics integration, and model-based parameter adjustment features are included.
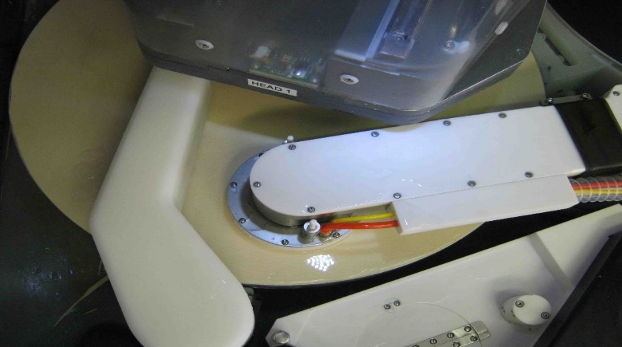
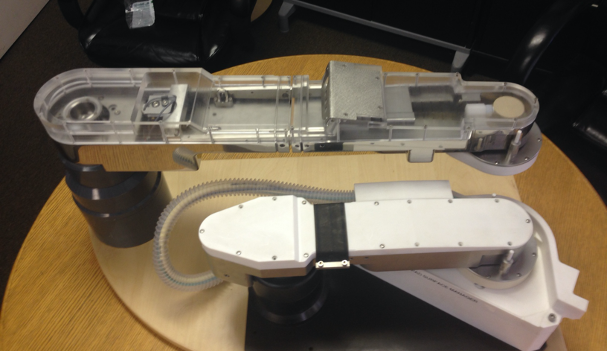
Our PSM enables Continuous Improvement and Lean initiatives expected by Automotive and similar IC Customers. Through available instrumentation and improved control of the slipstream the PSM can measure, analyze, reduce the variability and control all of the dynamic state parameters listed below in red.
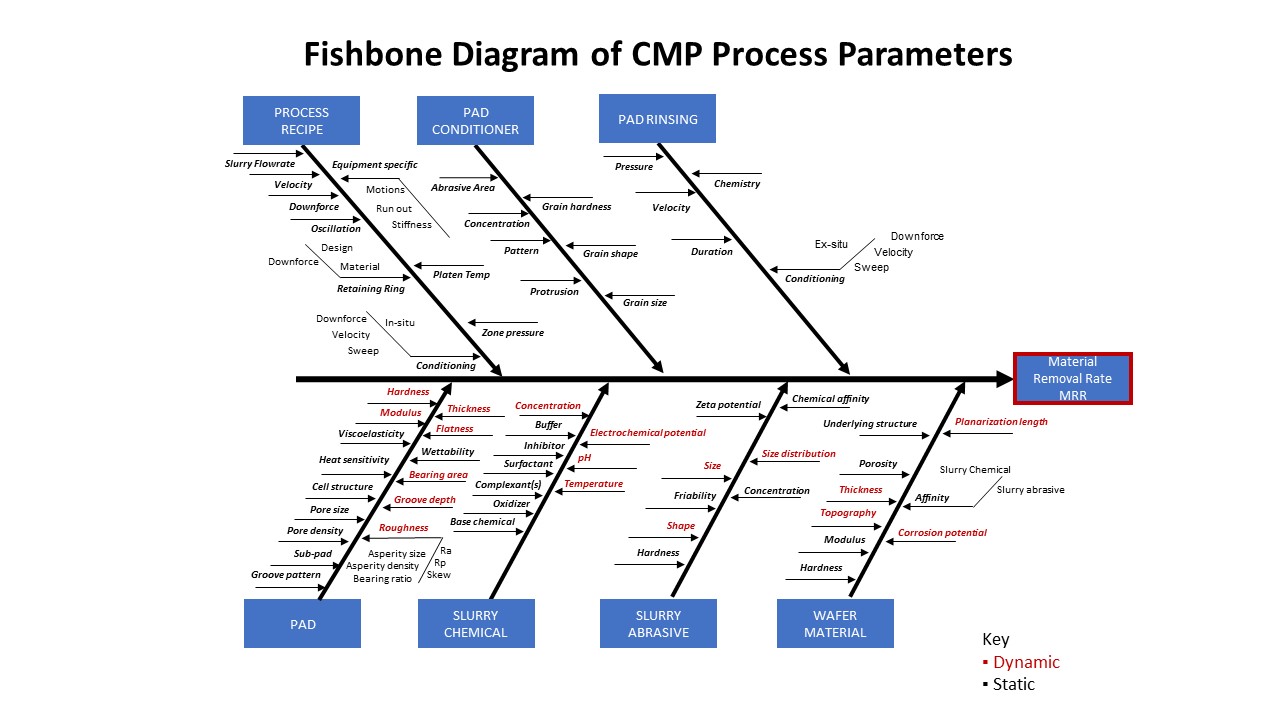
The PSM has been implemented using COTS components from industry leading suppliers to ensure reliability, maintainability, and service level.
PSM Availability
The Company offers licensed equipment designs, build to order systems, integration services, and evaluation units. Currently available for Applied Materials: Mirra, Reflexion, Reflexion LK.
Integration to other CMP platforms is straightforward, sharing much of the existing subsystems, software, and engineering. Projects will be undertaken with customer participation.